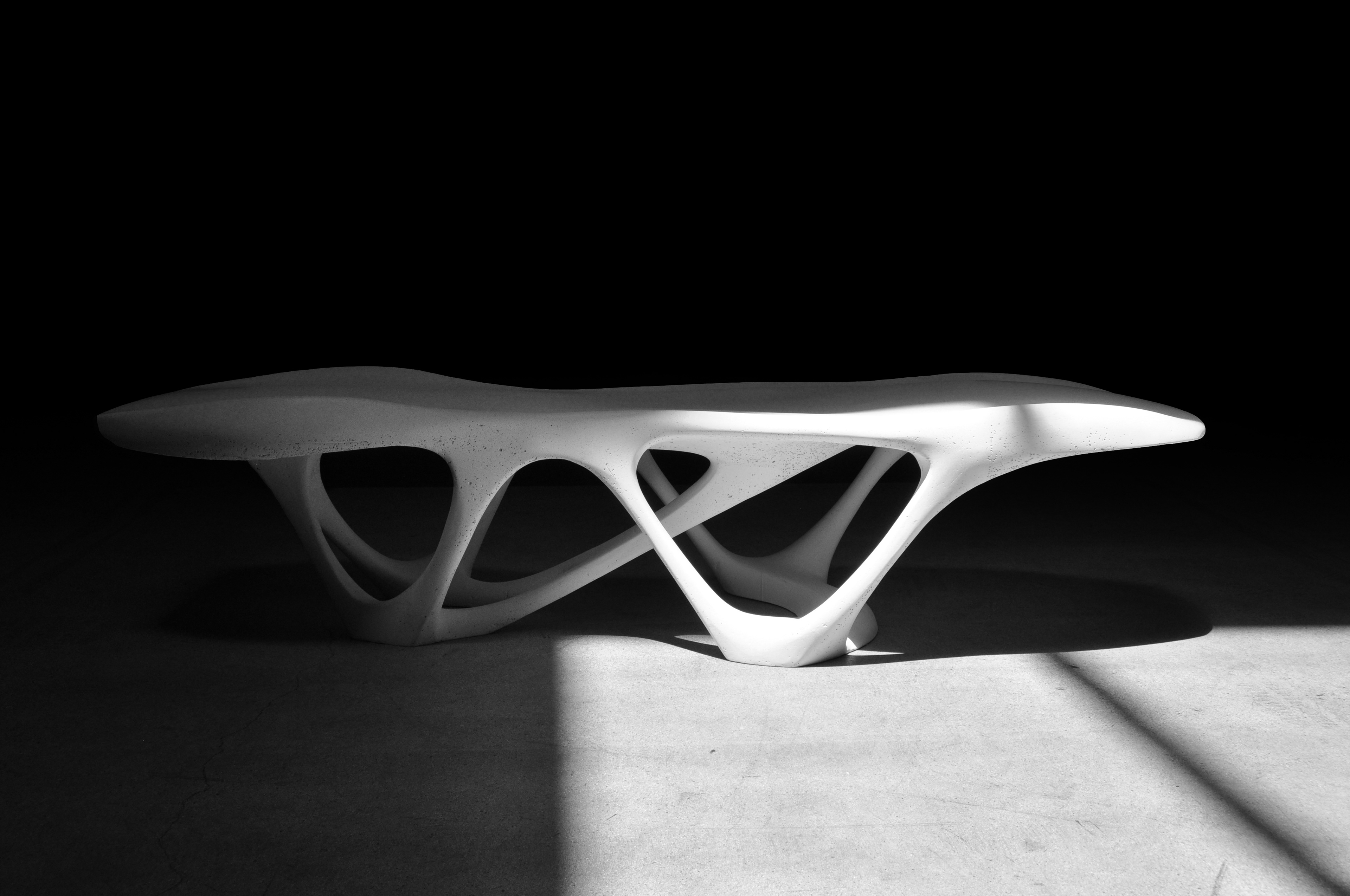
A concrete exploration using 3D printed molds with a goal to see how delicate, detailed and finite the material could get while still being structurally rigid. This project was for a proof of concept intended to be scaled up upon success. Ultimately the focus was to create a piece of furniture that embodies an optimal balance of delicateness in form and strength in density. 3D printed investment molds were used as a new way to realize concrete in the interest of pushing its natural limitation. Generative design and topological optimization tests were performed in Rhino and Fusion 360 alongside form-finding sculpting exercises done in Maya. This allowed for a substantial reduction in overall weight and freedom of form.
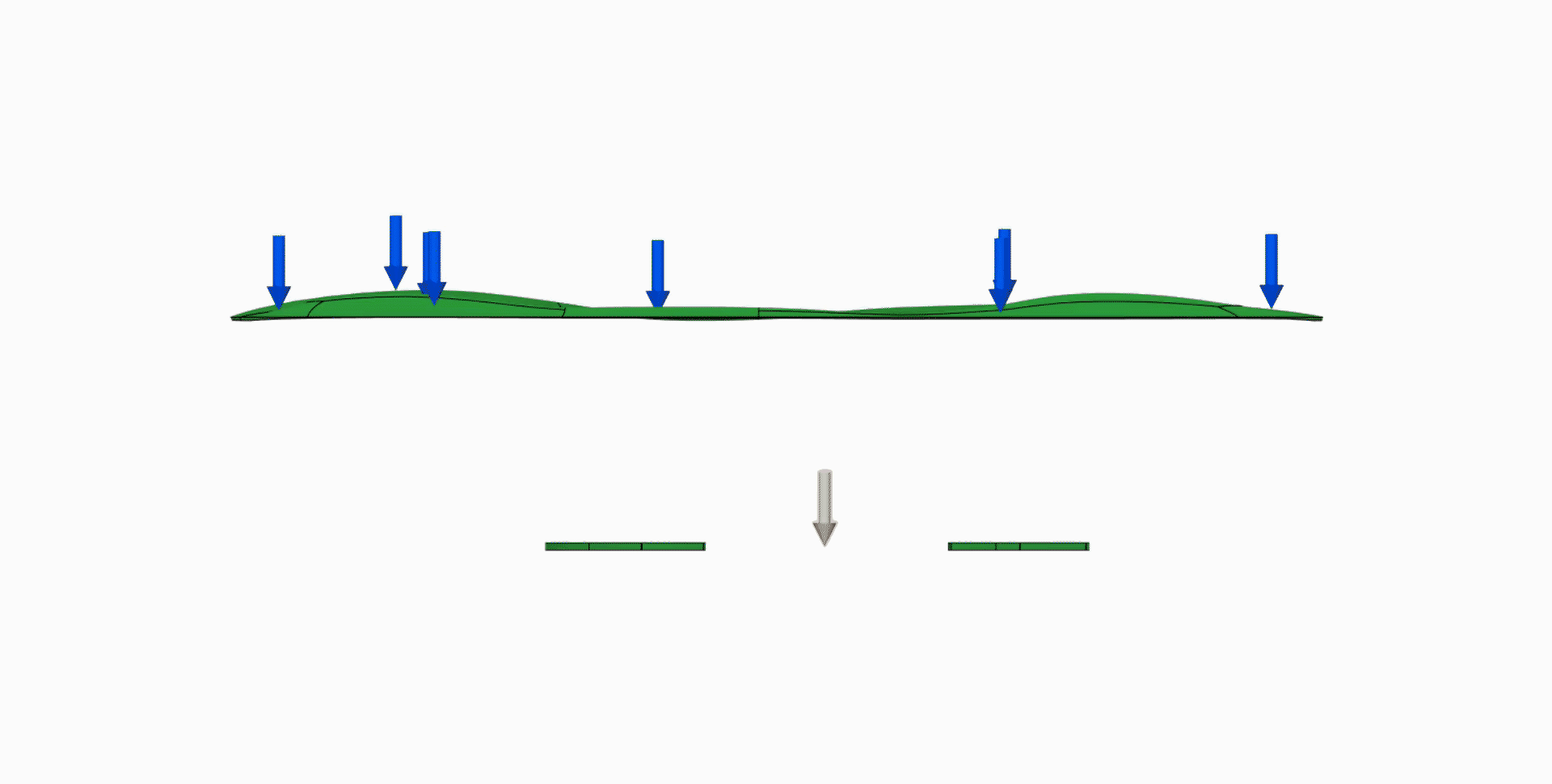
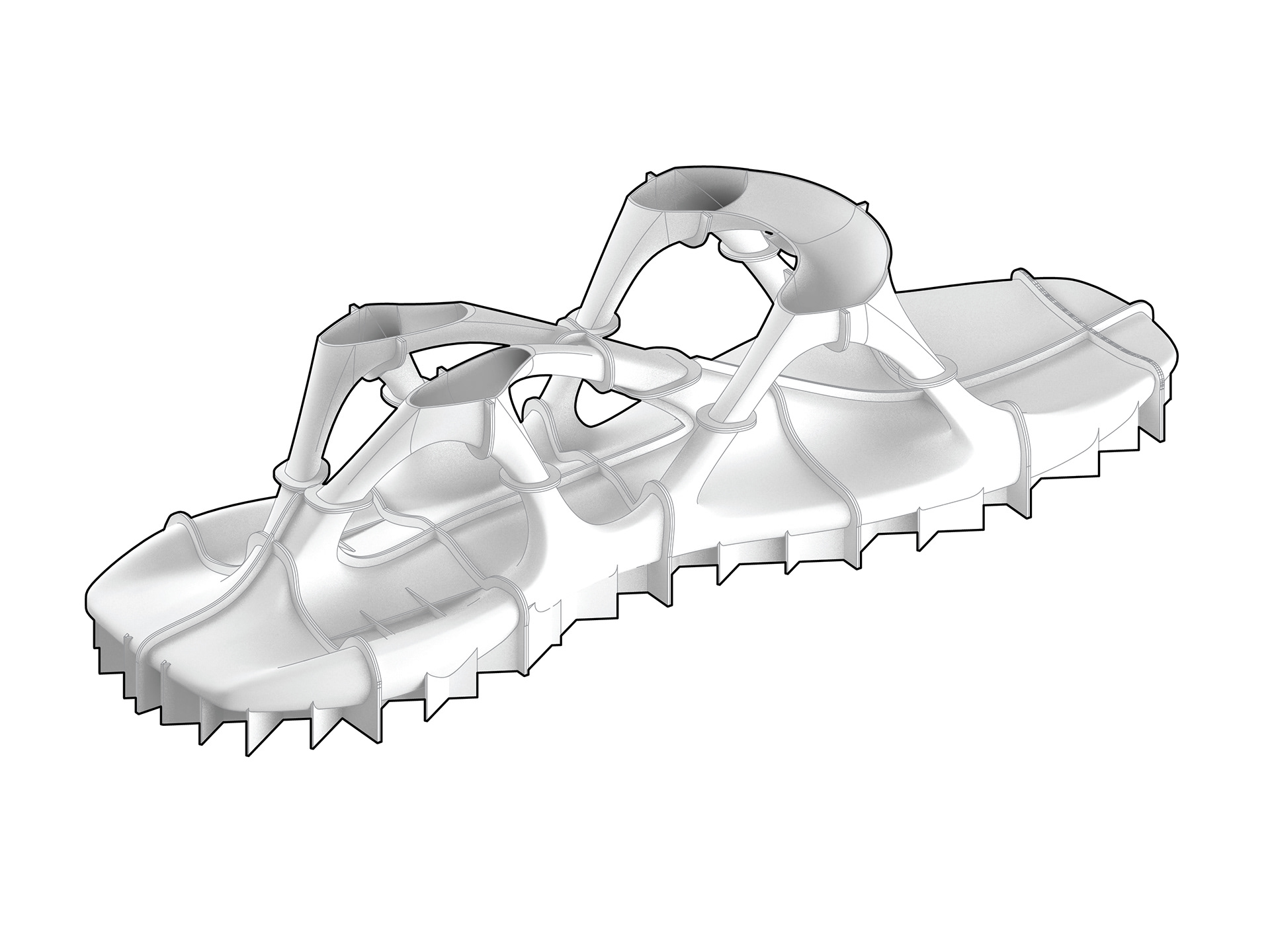
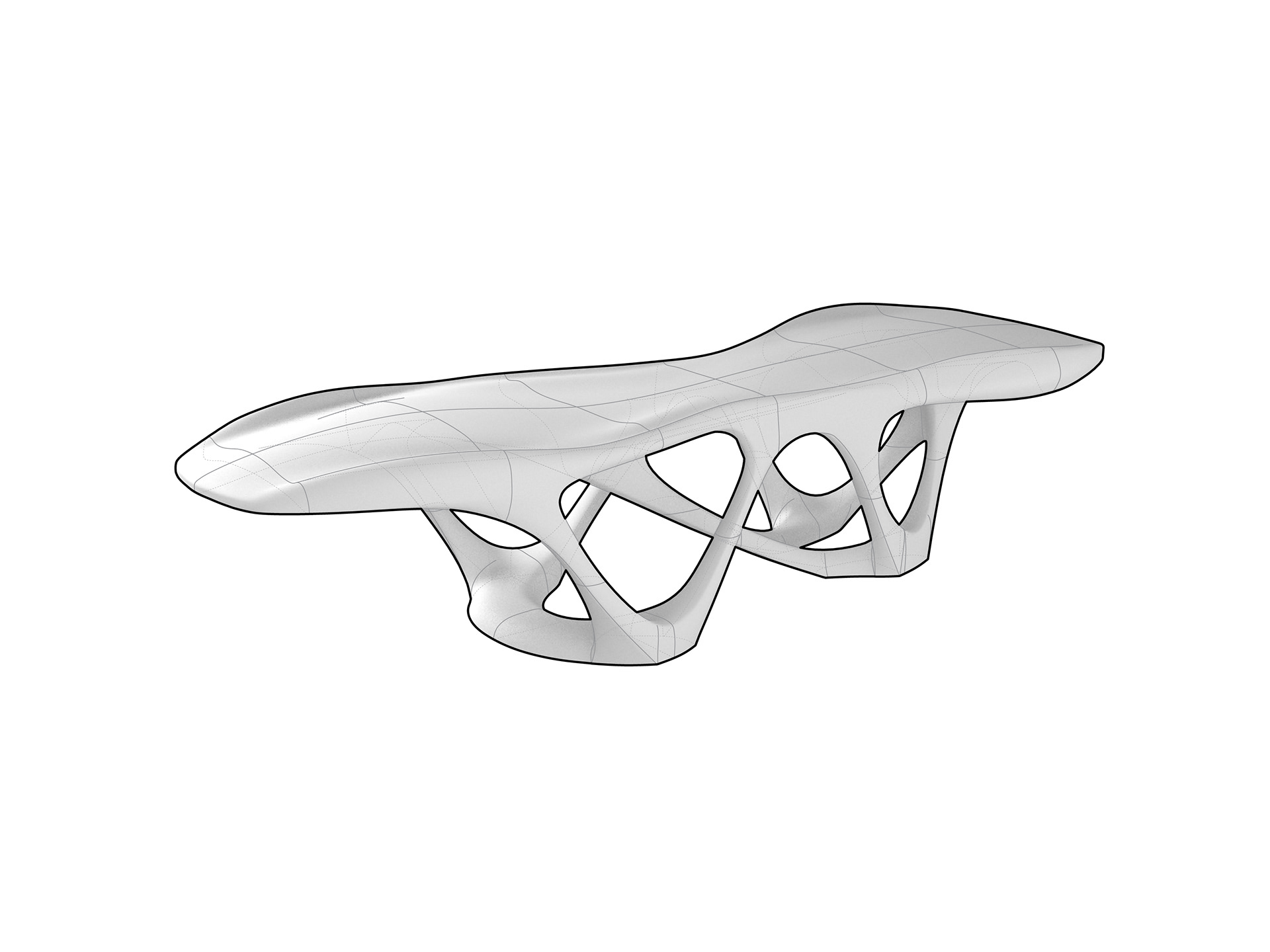
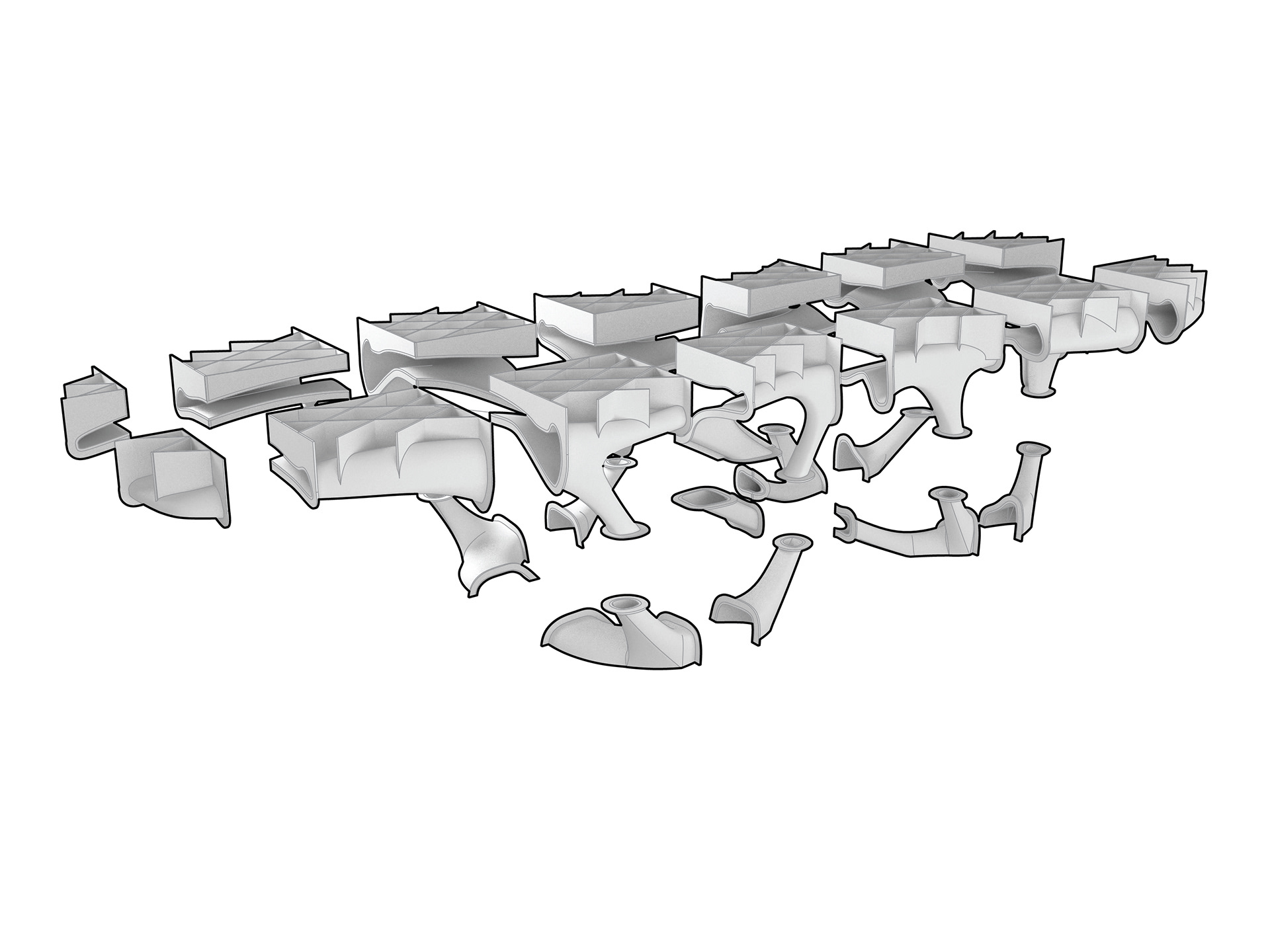

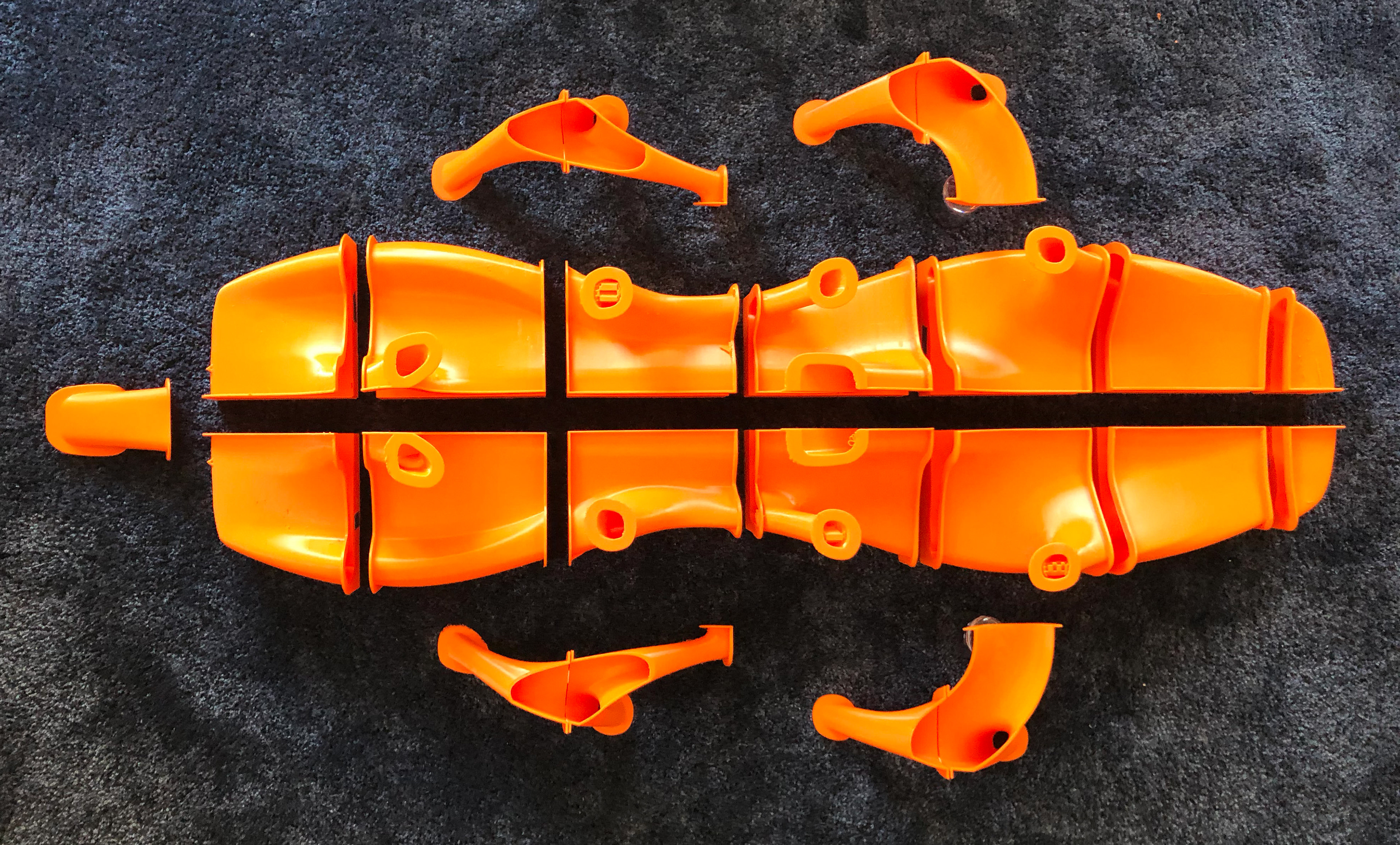
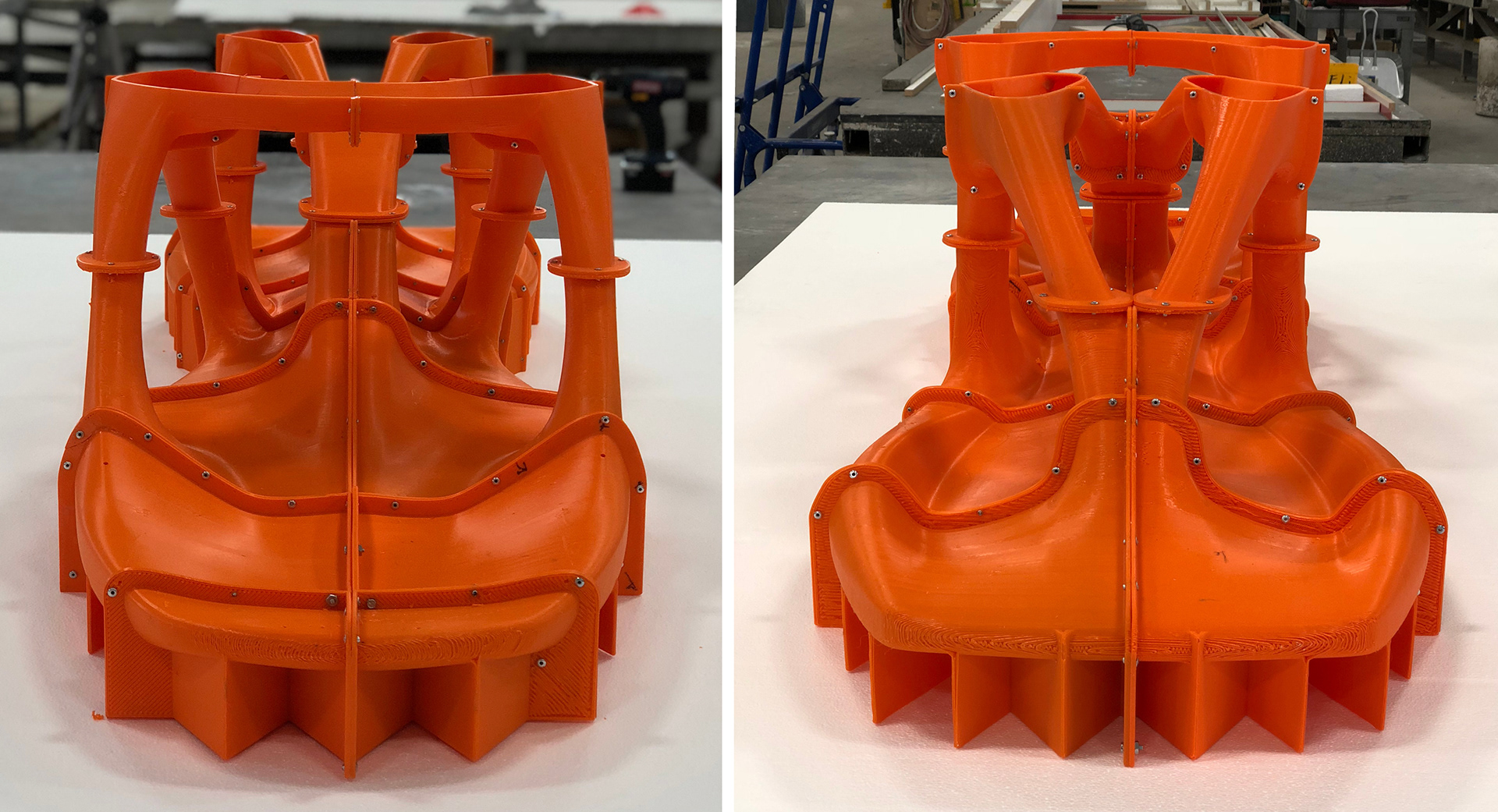
Twenty-three pieces of fiber-reinforced PLA plastic molds were created on a standard FFF printer with a blunt nozzle. Fastened together with steel nuts & bolts on the underside and steel rivets on the legs and base for speed of assembly. Even with absolute printing precision, the plastic can tend to crack, warp and often create uneven surfaces that require a lot of post-process work. The 5ft investment mold was designed to withstand up to 300 lbs of unreinforced Ultra-High-Performance Concrete while also being able to withstand the stress of a vibration table that was used throughout the pour to help settle the material into all the cavities.
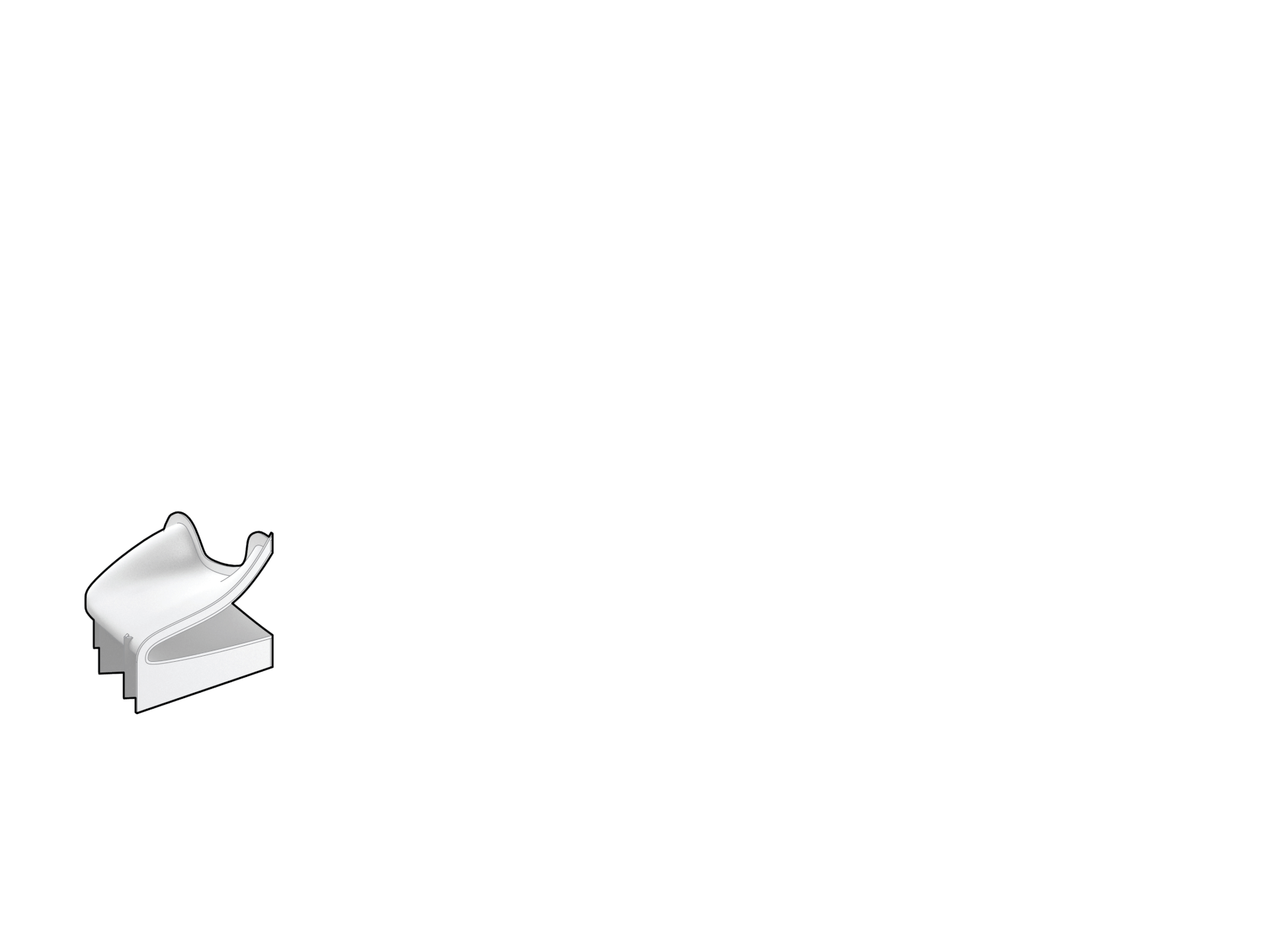
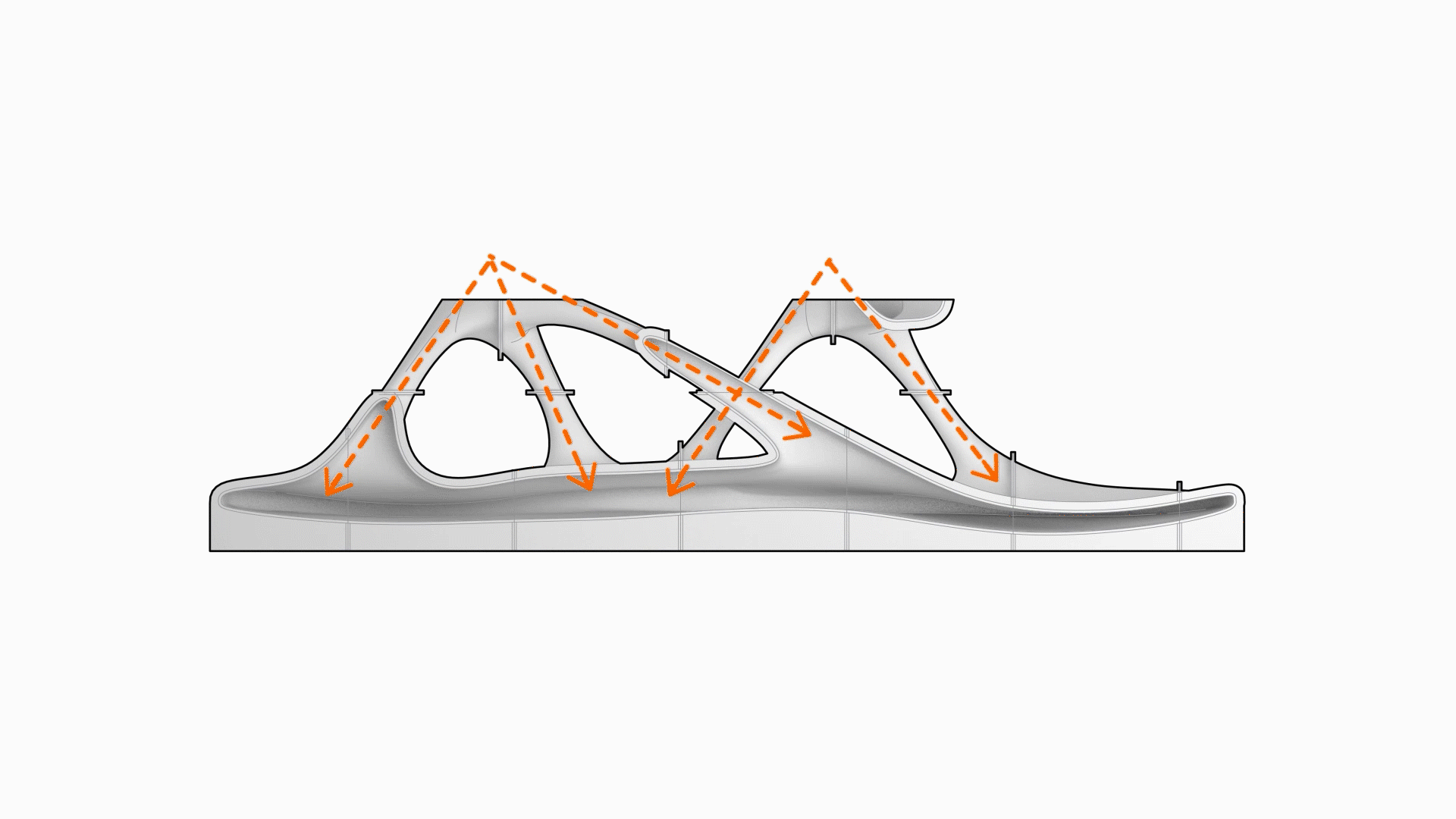
While assembling, the order proved critical in achieving a tightly sealed cavity. With intent to keep a porous underside and a smooth top surface, the mold was poured upside down. This also mitigated the overall stress on the mold and allowed for easy mold management during the pour. The concrete was fed into 3 major openings at the bottom of the 10 legs and flowed downward to fill the entire cavity. Once filled, the heat and off-gas stresses began to be noticeable. The sheer weight of the concrete on the mold and the hydrostatic pressure was enough to create many bursts in the plastic. The mold needed a substantial amount of repairs throughout the process. A stress-relieving drilling technique was used to alleviate these areas in combination with table vibration to reduce trapped air pockets.
The leaking concrete had to be secured immediately to avoid a ripple effect using tape, epoxy, zip ties, and clamps. This particular mold was designed to be a break-away mold to reduce the number of seams and overall printed pieces. With the assistance of the mold release, the removal of the pieces went relatively fast in areas that were less complex and flat while being troublesome in the areas with undercuts. The raw concrete surface retained all the lines found on the 3D print surface and later wet sanded smooth with diamond pads. This R&D project revealed many interesting findings over the 18-month process that will be used on the next scaled-up version that incorporates removable/reusable molds.
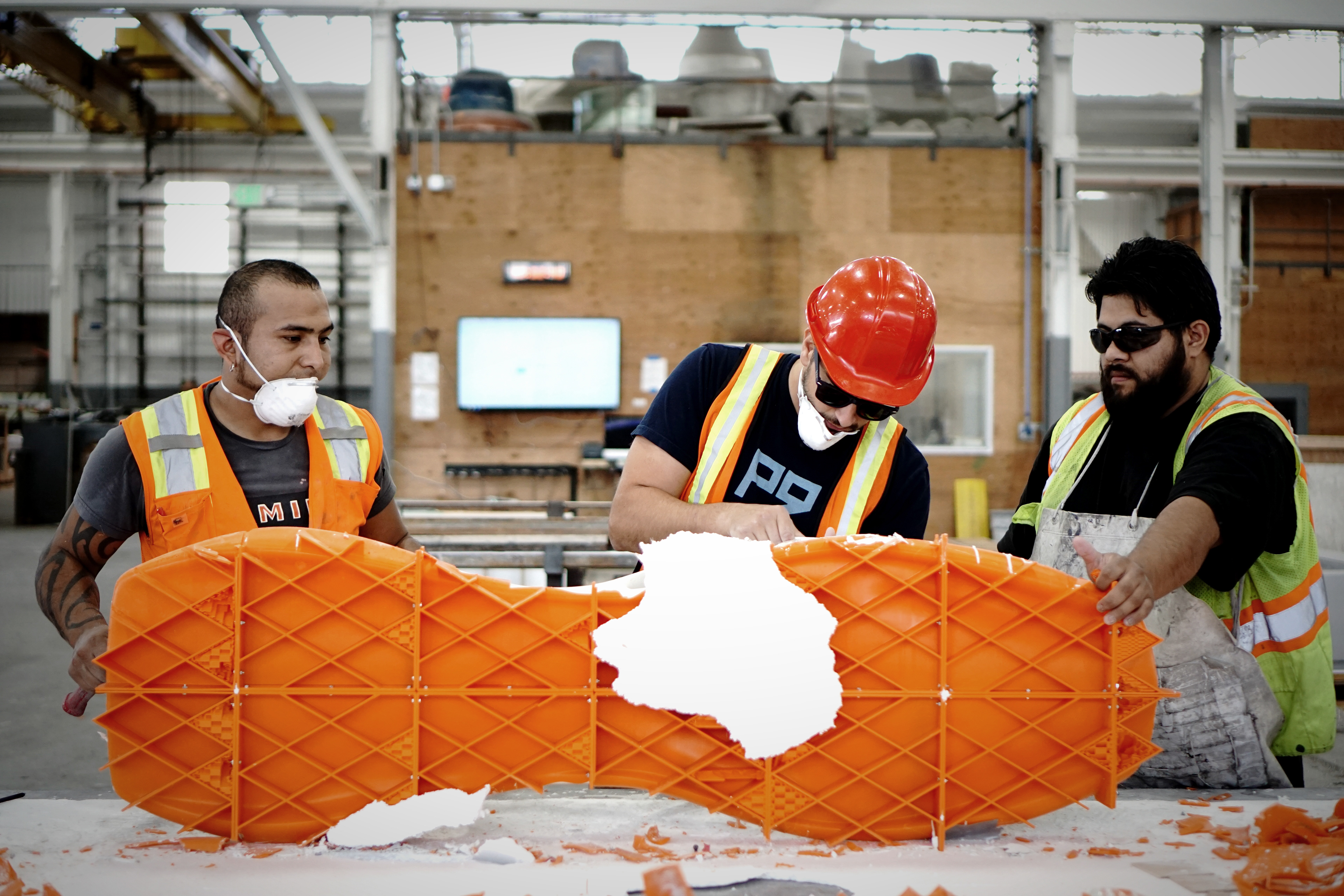
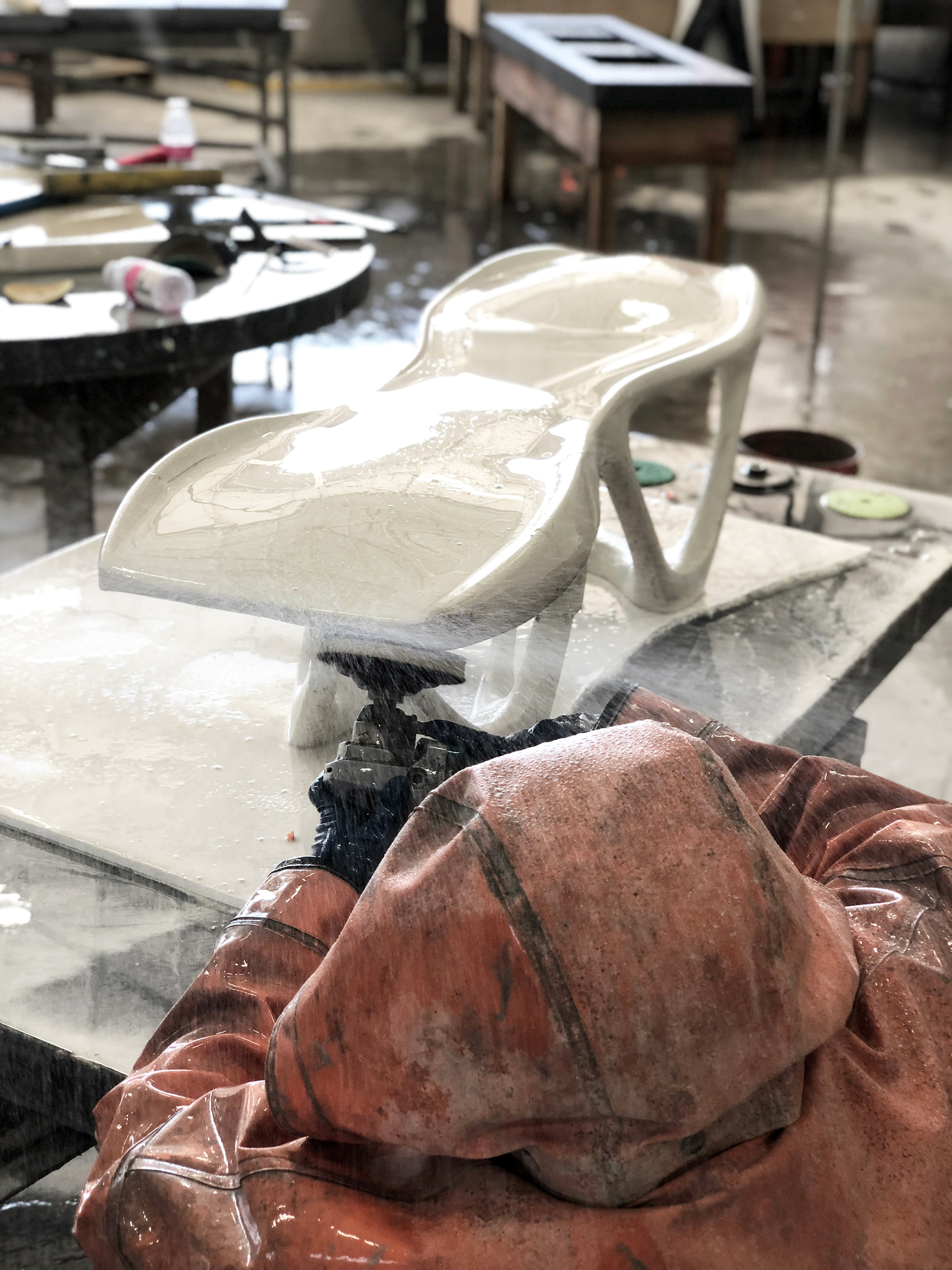
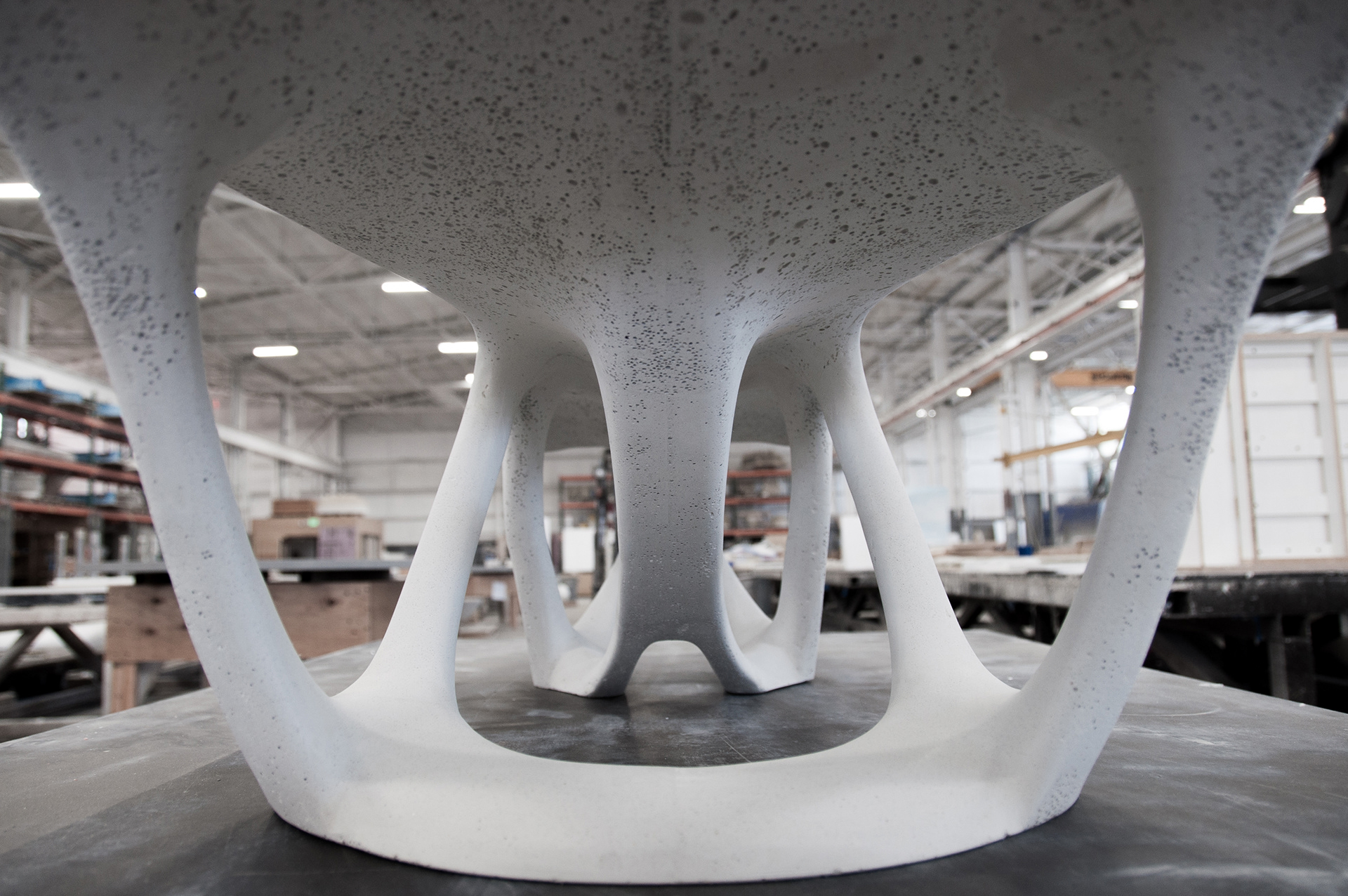
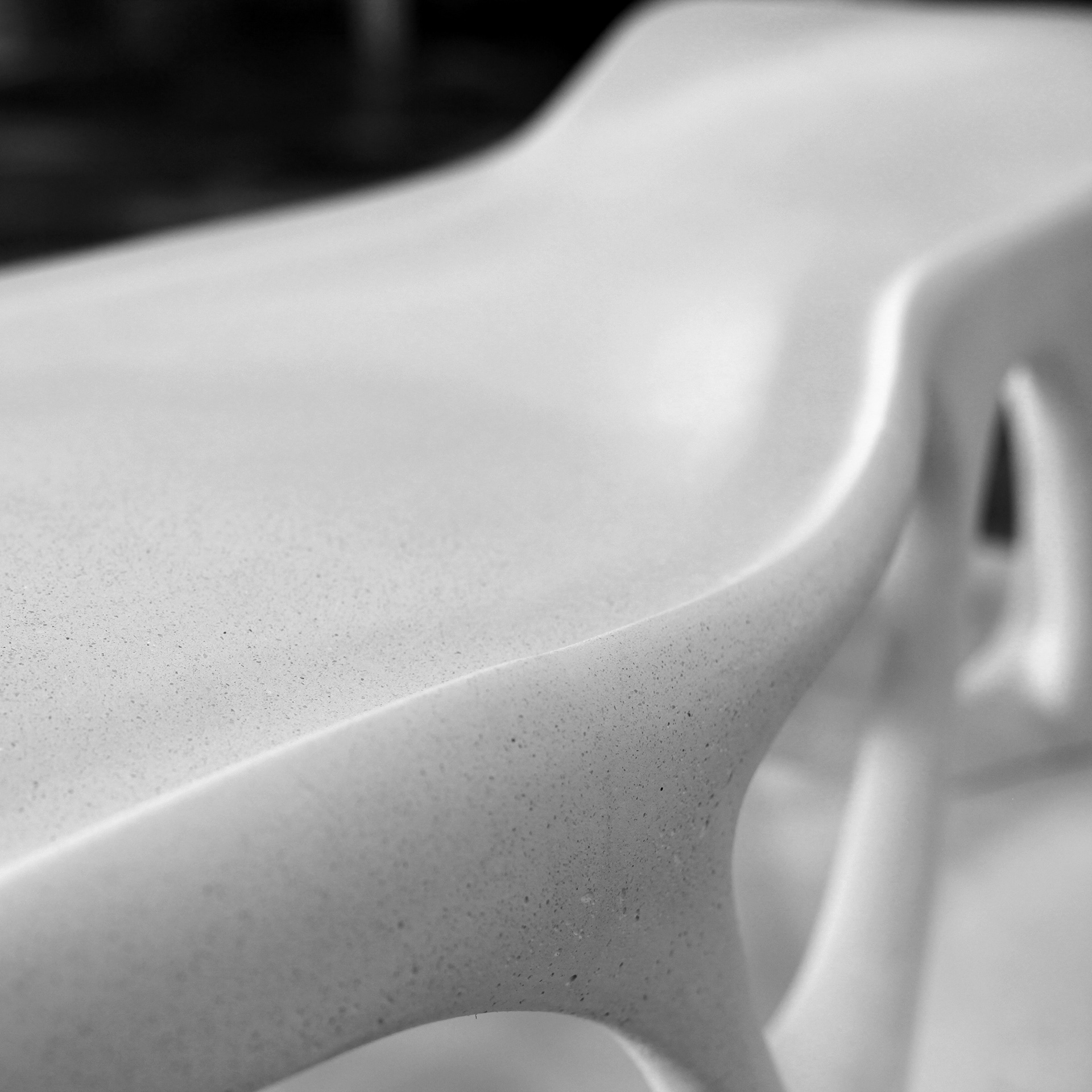
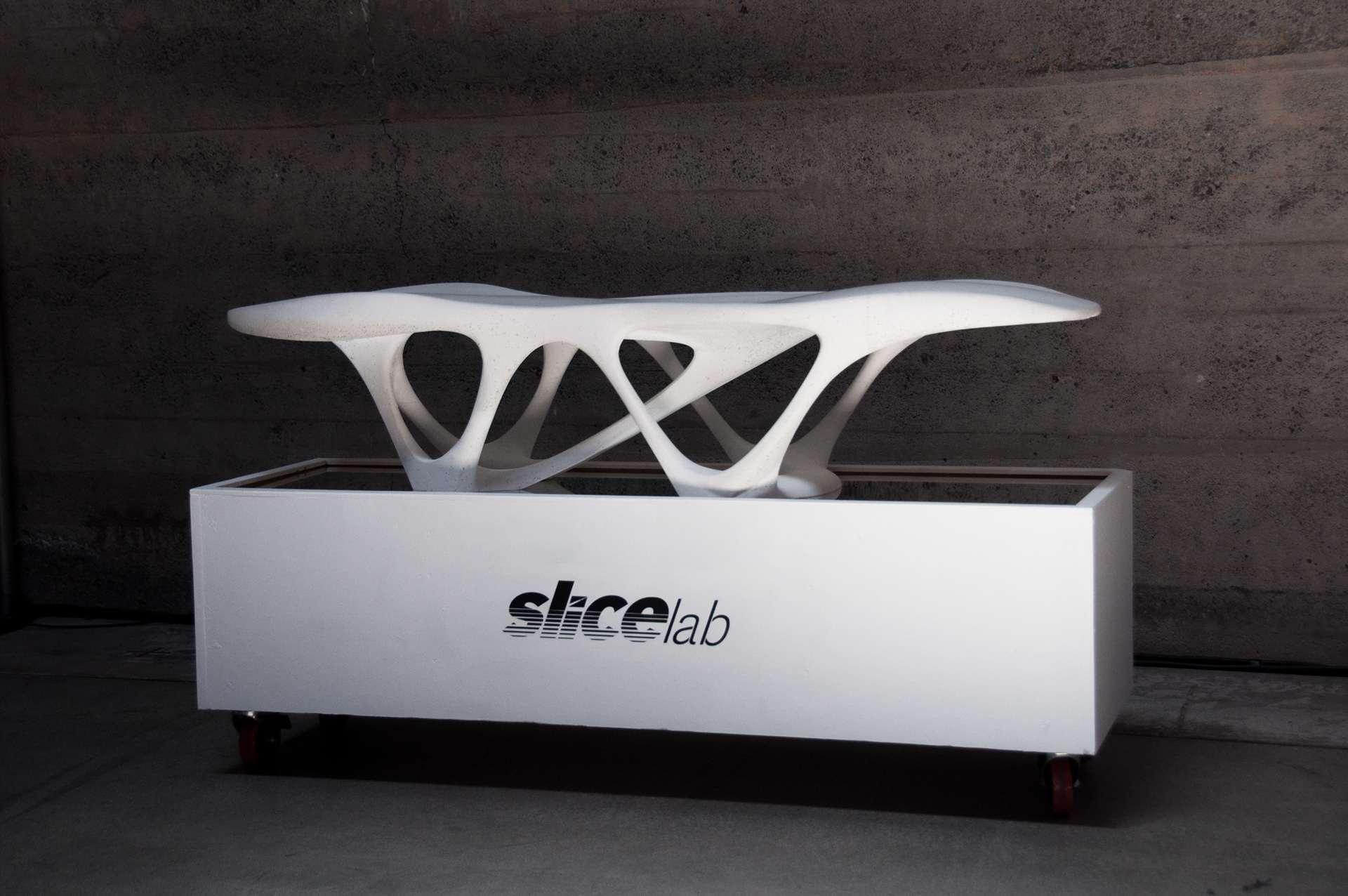
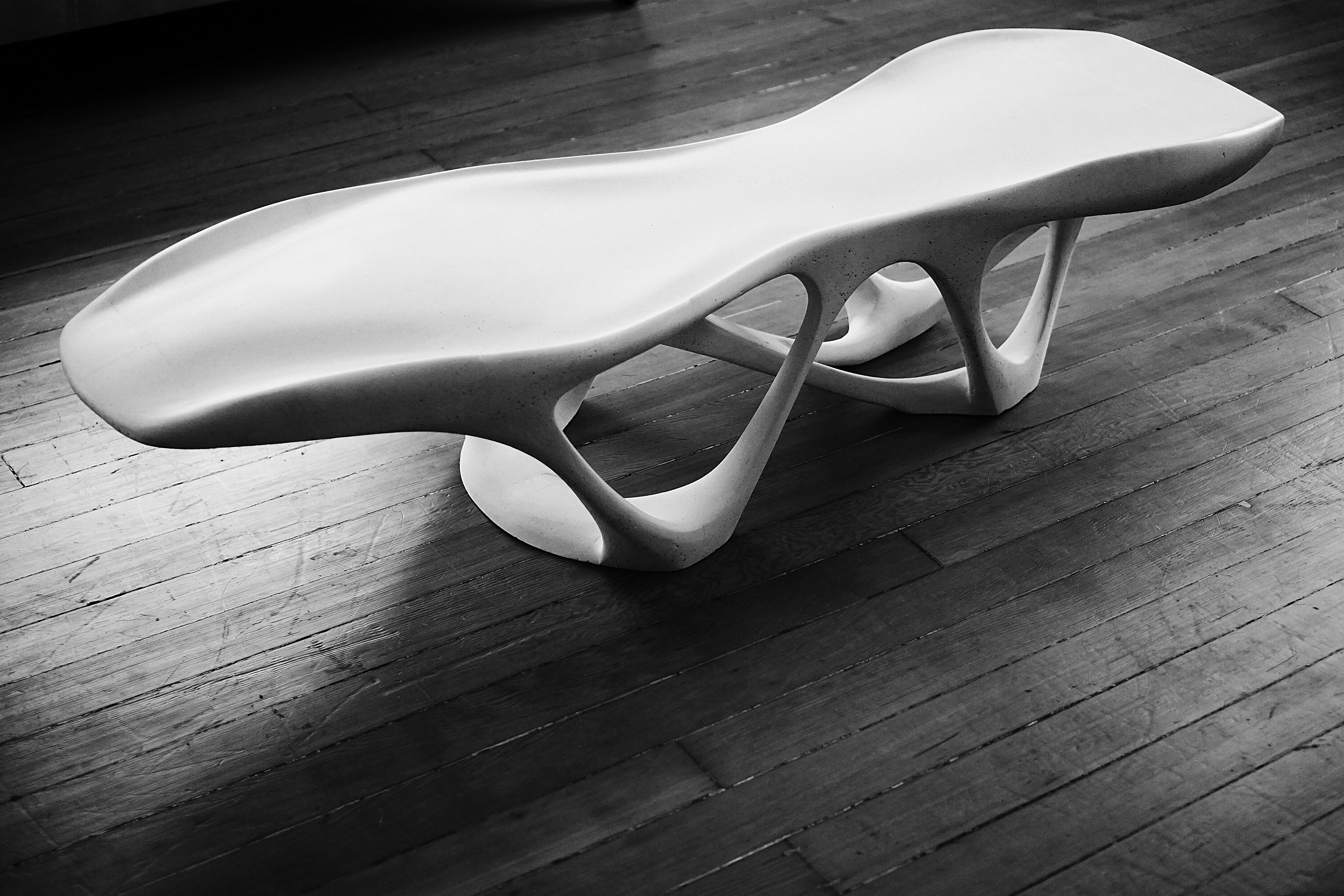
Process Images